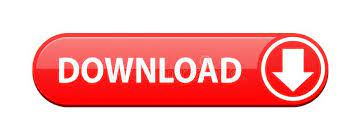
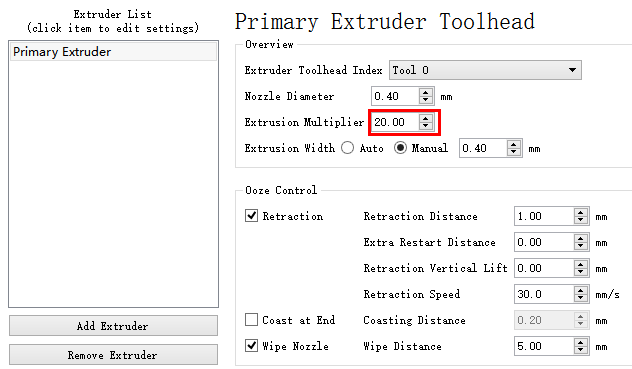
Its just a precaution I take and it has made a real difference in the quality of the surface finish. So filament will probably have some moisture. Even though we as manufacturers went to a lot of trouble to dry resins (ABS, PP, PVC, PMMA) prior to extrusion, the amount of drying can vary. I worked 25 years in a large German plastics extrusion company. I found I have to pre-dry just about all filaments when opened for the first time. Not sure it was really necessary though.Ģ. This gives a lot torsional strength/resistance to flexing without adding much weight and helps with assembly. For Wings and Fuselage I added 15% infill on the “Wing2per” process for the first 1mm of height. PETG is a little bit too flexible for flying so to stiffen the Ailerons, Elevator, Rudder and both stabilisers I added 2% triangular in-fill. (if printing at 0.2mm layer height then change the Extrusion multiplier to say 0.86 to 0.87 probably)īed Adhesion: Glue stick on PEI sheet (sticks like chewing gum in your hair). Printer: Prusa Original Mk2S with 0.4mm nozzle. Took a while, a lot of reading, but got it right after 2 days experimentation. Many holes at the start of a layer and bubbles within layers, but after experimentation I’ve had truely excellent results with “X3D PETG” (local Thai product but and any others will do) printing the “Edge”. I had many issues issues at first with PETG. At first tried the ultimate material polycarbonate, then tried PETG.
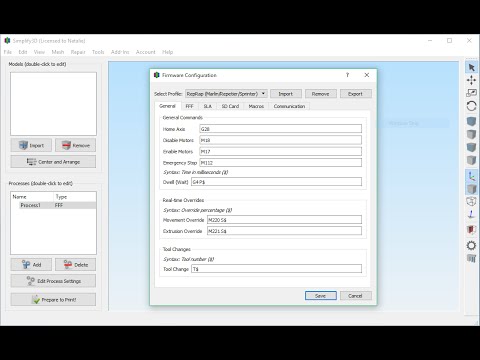
Hi, Living in a hot sunny climate (Sydney AUS and BKK Thailand) I needed to find a more temperature resistant and stronger material than PLA.
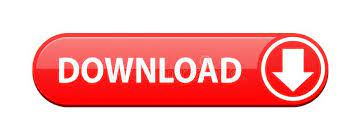